Company Profile
会社概要
- 社名
ゼオンメディカル株式会社
- 資本金
452 百万円(日本ゼオン株式会社100%出資)
- 従業員数
209名(2024年4月1日現在)
- 本社住所
東京都千代田区丸の内1-6-2
新丸の内センタービル - 設立
1989年5月1日
- 事業内容
医療用機器の製造・販売
- URL
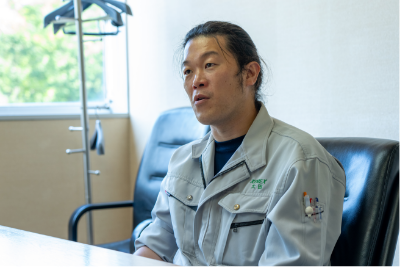
WMS導入プロジェクトリーダー
太田 鉄矢 氏
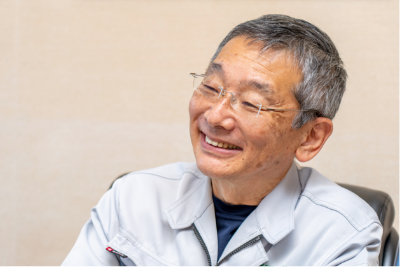
生産管理グループ長
原 信行 氏
Company Profile
ゼオンメディカル株式会社
452 百万円(日本ゼオン株式会社100%出資)
209名(2024年4月1日現在)
東京都千代田区丸の内1-6-2
新丸の内センタービル
1989年5月1日
医療用機器の製造・販売
WMS導入プロジェクトリーダー
太田 鉄矢 氏
生産管理グループ長
原 信行 氏
ゼオンメディカル(株)は、化学メーカー日本ゼオン(株)の関連会社として1989年に設立された。循環器系、および消化器系製品を柱として、医療器器の研究・開発・製造・販売までを一貫して行っている。国内グループ会社14社と連携して、体内の血液循環を補助する大動脈バルーンカテーテルや各種カテーテル、内視鏡を用いて胆道の狭窄を改善する胆道ステント、結石除去のためのバスケット、クラッシャー等の治療デバイスを病院や医療機関へ提供している。医療従事者や治療を受ける患者の立場に立った製品を世に送り出している。
製品①IABPバルーン MEISHU® sensor
製品②IABP コンソール ZUIRYU®
IABP(Intra Aortic Balloon Pumping)とは、心筋梗塞や心臓外科手術に伴った心原性ショックおよび低心拍出量状態の際、心臓のポンプ機能を補助する方法の一つです。
バルーンカテーテルを大腿動脈から挿入し、胸部下行大動脈に留置し、動脈圧または心電図の周期に合わせてバルーンをヘリウムガスで収縮・膨張を繰り返すことにより、ダイアストリックオーグメンテーション効果とシストリックアンローディング効果を促して心機能の回復を行うシステムで、現在国内では年間約2万症例前後、使用されています。
ポンプ駆動装置「IABP コンソール ZUIRYU®」に接続して使用される「IABP バルーン MEISHU® sensor」は、日本人の血管径、血管長から設計された従来品「IABP バルーン MEISHU®」に、新たに光センサを搭載。国産メーカーによる初めての光センサIABPシステムの導入となります。 光センサにより遅延の少ない正確な血圧のモニタリングが出来ることから、心臓の周期に合わせたより的確な駆動が可能となり、駆動応答性の高い「IABP コンソール ZUIRYU®」とのセット使用により、治療効果の向上が期待できます。
物流の効率化への取り組みの中で、弊社のWMSも導入して頂きありがとうございます。御社で進めておられる自動化やデジタル化の取り組みについて具体的に教えていただけますか?
インターストックの前に使っていたシステムは、情シスの方で作ったものでした。そのシステムで使っていたハンディが廃番になるという話があり、廃番になったら壊れた時に修理ができないので、それを機にシステムを新しくしよう。どうせ変えるなら、今困っているところを機能として組み込んで、新たに構築していこうとしたのがきっかけですね。
その時は、ハンディの老朽化への対処や、生産性を向上させる取り組みの一環としてのロケーションフリーや作業進捗の可視化など、業務的に分断していたところをシステム化して、連携を強化することなどを目的として上げておられましたね。
その通りです。あとは間違い防止ですね。前に使っていたシステムには目視で確認する箇所が多々あったので、新しいシステムではなるべく少なくしたいという思いもありました。物流展でお話を伺って以降、数ヶ月をかけて3社のWMSを比較検討しました。
弊社をお選びくださったのはどういった点からでしょうか。
営業担当者が良かったからですよ(笑)。正直、金額はインターストックが一番高かったんです。しかし、最終的に他の2社と比べて見て、1社がASP型で、もう1社がインターストックと同じオンプレ型だったのですが、どうしても弊社独自の要望をASP型では賄いきれないことが見えて来たことが、インターストックに決めさせて頂いた一番の理由です。。ASP型のデメリットのひとつとして、通信の問題があります。読み取って処理するのに少し遅いと感じたので。
物量が多いときに通信の停滞があると、製品が出荷できないのでとても困ります。そこで停留してしまうと、梱包の手前に注文書だけが山のように残ったりしますからね。一瞬で処理してピッキングできると都合がいいのです。時間帯によって出荷の量に波があるので、波が高い時にトラブルが来たらどうしようもありません。その日のうちに出荷できないという、最も恐れている事態になります。通信速度というのは非常に重要です。その点では、インターストックが優れていました。
プロジェクトを進める上でどんなところに苦戦されましたか?
コロナ禍で、現場を見てもらった上での説明ができませんでした。そのあたりが一番苦労したところでしょうか。
性能記録を残すシステムには携わったことがあったのですが、私がシステムプロジェクトを担当するのはほぼ初めてでした。大きな予算をかけてシステムを導入していくことに、やはり不安はありましたね。でも、そう思ったのは最初の段階だけで、その後は莫大な金額に対して何年間でペイできるのか、というデータをひたすらかき集めました。そういう意味では、問題は予算面だけでしたね。製品と部品は分けて開発を進めましたが、敢えて分けておいて正解でした。部品倉庫の実稼働これからですが、製品倉庫から先に進めたのは正解でした。製品倉庫の方は実作業にも関わったことがあって、内容が把握できていたのでやりやすかったです。部品倉庫は最終段階まで来ており、あともうひと頑張りです。
現場を見ないと、入出庫の実際がなかなか伝わらないですよね。
現場で細かい作業をやっているのが後から分かって、軌道修正したりしたことが大変でした。導入時には今までと全く違うことをするので、作業者には不安があると思うのですが、そこを納得してもらうことにも気を遣いました。一時的に両方のシステムを使わなければならないので、苦労したと思います。
システムが安定稼働するまでに、現場で苦労されたことはありますか?
一番苦労したのは、今日からやるぞっていう前の在庫整理だとか(笑)、切替えのタイミングでした。でも、オンザリンクスさんの対応のアクションがとても速かったのでそこまで苦労は感じなかったです。Xデーを決めてあとは人海戦術です。導入の翌日からはちょっと不安もあったので、現場に張り付いて運用を確認しました。現場の運用も早く慣れていったと思います。
現場の方々のインターストックの印象はいかがでしたか。
とても良いです。私の印象でも倉庫は常に一杯だったのですが、フリーロケーションになったお陰で、今は1/3のスペースで作業ができています。また以前は結構残業がありましたが、今はほとんど残業をしていないです。「もう今日は出荷ないの?」という声も現場から出て来るようになっているので、それはシステム導入の効果だと思っています。
当初思い描いていた作業の効率や生産性についてはいかがですか?
狙っていたフリーロケーションと業務効率化は目に見えて良くなりました。確認の回数自体が減りましたし、目視より確実なので出荷ミスも減りました。色々な効果が上がっています。
部品倉庫は導入に向けての作業を進めていますが、稼働している製品倉庫について、拡張も含めて今後どのようなことを期待されていますか?
以前もご相談したように、まずは返品物流ができればいいと思います。あとは製品倉庫導入当初から考えていたのですが、日本通運の送り状番号と弊社の伝票番号を照合できたらより便利になると思います。
究極的には、ボタンを押したら全て完全自動化できるのが理想です。
製品倉庫を2021年3月に納品させて頂いて、安定稼働まで数ヶ月掛けて準備を進めました。半年一年ちょっと間を空けて、製品倉庫が安定して来たタイミングということで、2022年7月に部品倉庫のスタートを目指して進めさせて頂いています。製品倉庫とは、取り組みも現場のチームもガラッと変わりました。部品倉庫の立ち上げプロジェクトについて苦戦されたことお聞かせください。
製品倉庫は発送先が色々あっても、倉庫から出して病院に納めるというルールは一つです。部品倉庫は7個ラインがあって、ラインごとに少しずつルールが違っていたりします。その点はちょっと不安に思いました。7つ別々のシステムを入れるとお金がかかるので、そこをいかに一つのやり方に落とし込んで作っていくかということが、苦労というか不安でした。あとは製品倉庫よりも部品倉庫の方が経験が浅かったため、私が出している要件で本当に網羅できているかのか気がかりでしたね。かんばん運用や在庫移動、もしくは生産実績で在庫を落とすなどを、どのようにシステムに落とし込んでいくか、不安と戦いながら進めてきました。
製品倉庫の後なのでやりやすいかなと思いましたが、部品倉庫には部品倉庫のやり方があって、そういう訳にはいかなかったですね。
製品倉庫の経験を活かして御社に説明できるので、やり取りはスムーズでしたね。製品倉庫の事例に基づいて要望を出せたのが良かったです。あとはすでにインターストックをさわっていたので、自分自身が理解して、他の人に説明することができました。共通言語ができたところで、複雑な部品倉庫の方に取り組めましたから、導入の順番としては正しかったなと思っています。